Benefits of Ultrasound Technology
- CTRL Systems
- Jan 11, 2022
- 3 min read
Ultrasound is instantaneous. There is no waiting for an expert to get back with you once they’ve reviewed the data or oil sample that you sent. Ultrasound is nondestructive. You can test while the equipment is operating.
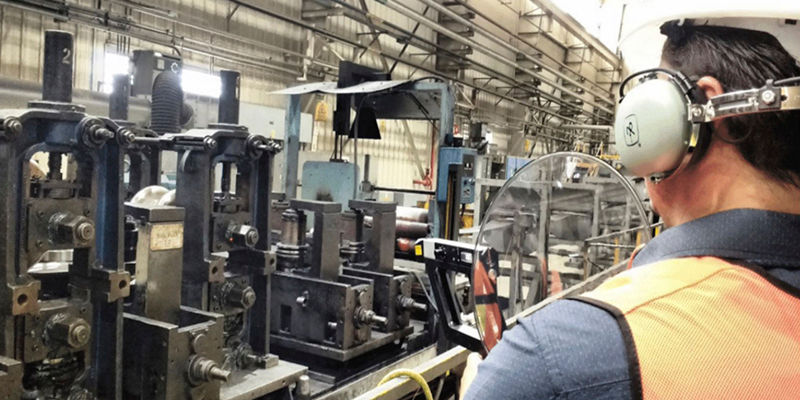
The last thing you want to do is stop your equipment from making money. Ultrasound is versa-tile. Not only can you put the UL101 receiver in the palm of your hand, but you can also carry it with you on a belt pouch along with several attachments. There are many, many applications!
Ultrasound is inexpensive to implement. Many companies have already spent lots of time and money on predictive and preventive maintenance technology and programs. You can incorporate ultrasound into your program without any major changes. Ultrasound is easier to learn and use. Nobody trained you how to hear. The same applies to ultra-sonic inspection. You will know if the sound of your equipment is not normal. However, CTRL does offer training to assist with proper implementation of the technology, so you know and understand the different applications and techniques for using ultrasound. Ultrasound is more accurate at pinpointing problems.
Ultrasound stays close to its source and does not tend to travel around corners. Finding and pinpointing leaks or identifying failing components is the result of the physical nature of ultra-sound. Finally, ultrasound pro-vides the earliest warning. Wouldn’t it be nice to schedule repairs before losing millions of dollars in unscheduled downtime because a bearing or gearbox failed?
In-Depth Look at Bearings
Let’s look at this in some more detail because critical bearings cost companies billions of dollars every year in lost production due to unscheduled downtime. Let’s say the expected life of a bearing is three years when properly in-stalled. It would be expensive and time-consuming to change every bearing once three years have ticked away. You want to get the most you can out of each component. Ultrasonic testing will indicate whether or not the bearing is still in good condition. Maybe, this bearing will last for a couple more years.
Many bearings fail early in their lifecycle because they were im-properly installed – causing excessive wear and misalignment of the shaft. Now, three years is looking more like six months. Ultrasound is used to verify proper installation and to ensure you get the most out of each bearing.
Electrical Systems
Using ultrasound technology has saved time and money for even electrical systems. Arcing in the windings or at the insulation of small transformers causes failure in power supplies, PLC actuators, and more. Shellac used for insulation of the wire can become damaged in assembly or has been misaligned causing arcing. The UL101 is used to scan the components and determine if electrical arcing is occurring, eliminating previous testing methods requiring unnecessary destruction of these components.
Electrical systems are often difficult to troubleshoot. Electrical motors go bad because of the bearings, bushings, or brushes. The ignition system or alternator is bad on the car or truck. The spark plugs aren’t firing properly, the relay boxes are bad, there’s corona discharge, etc.
Electrical arcing produces ultra-sound. It does not matter if it’s the spark plugs in the car or the transformers at the switching station. Misfiring and arcing are easily detected. Just don’t use a metal extension. The UL101 comes with a polycarbonate ex-tension rod.
Non-Pressurized Cavities
In situations where the integrity of a non-pressurized, sealed cavity is critical, an ultrasonic transmitter can be used in con-junction with the receiver to lo-cate cracks, gaps, or holes in the walls or seals. These faults do not naturally produce ultrasound. A transmitter is used to fill the space with ultrasound so that defects can be located with the receiver.
Inspection with ultrasonics is often easier and more effective than standard procedures that require methods such as hydrostatic testing, soap and bubble testing, and pressurizing with air. For example, the seals around the windows and doors of the military’s KC-135 air cargo tanker cannot have any cracks or holes. According to procedure, the KC-135 must go through a 10.9 pressure drop down test to ensure that cabin pressure is maintained at high altitudes. Just because the tanker passed the drop-down test does not mean there aren’t any defects. Ultrasonic technology is used after the drop down test to verify the existence, or lack, of defects.
An easy solution is to turn on the UT2000 Universal Transmitter, place it into the cabin, close everything up, and use the UL101 receiver to listen for the strongest ultrasound signal, which indicates the location of the defect. This works a lot better than dunking the tanker in water, and it also helps pinpoint failures that are easily missed with other tests.
The US Army has the UL101 and UT2000 in several tool kits for wheel and track vehicles and use the technology for both testing of non-pressurized vessels for Nu-clear-Biological-Chemical (NBC) related testing, and for testing the operation condition of hydraulics, gears, bearings, and more.
Comentarios